Boric acid has multiple uses in several industries, the pharmaceutical, glass, ceramic and cosmetics industries being some of them. Boric acid, also known as orthoboric acid or hydrogen borate, is a chemical compound that can be produced through a series of chemical reactions. One common method for its production involves the reaction between borax (sodium borate) and sulfuric acid, resulting in boric acid as the desired product and sodium Sulphate (Na2SO4) as a byproduct.
Sodium Sulphate is a white, crystalline solid and has various industrial applications, including use in detergents, textiles, and paper production. Depending on the purity and market demand, the sodium Sulphate byproduct may be further processed or sold to industries that can use it.
To separate Sodium Sulphate from the liquid solution resulting from the reaction to produce boric acid, you can use a variety of techniques: (cooling) crystallization, evaporation, addition of precipitating agent, electrolysis, ion exchange. The choice of method depends on the specific requirements and constraints of the separation process. Factors such as energy consumption, equipment availability, the concentration of Sodium Sulphate and the desired purity of the separated Sodium Sulphate will influence the selection of the most appropriate technique.
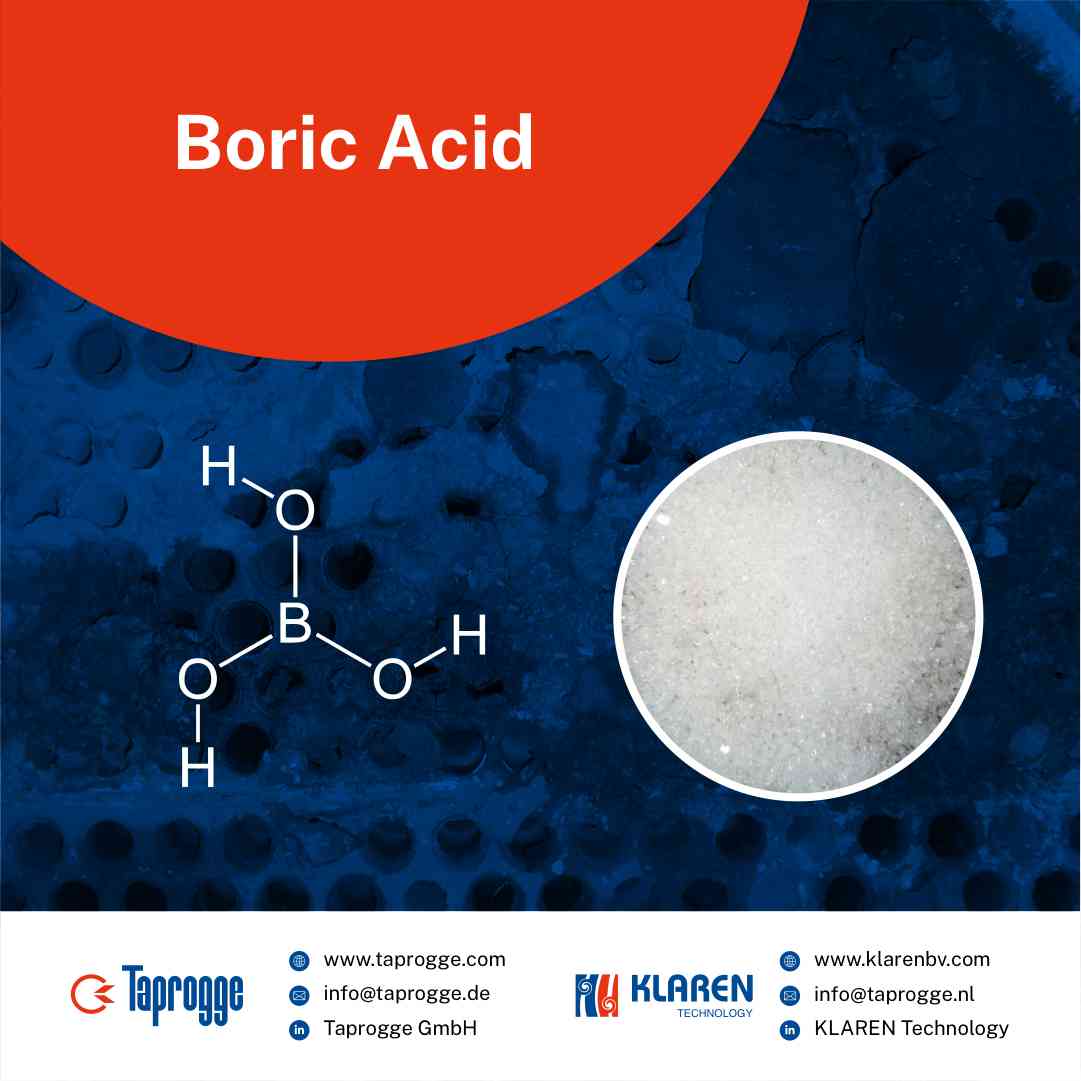
Crystallization, is one of the most common methods for separating salts like Sodium Sulphate from a liquid solution. The solution is heated to evaporate the water, leaving behind solid Sodium Sulphate crystals. The crystals can then be separated from the remaining liquid by filtration. This process can be repeated if higher purity sodium Sulphate is required.
Fouling is a common issue in industrial separation processes using evaporators or crystallizers, including the separation of Sodium Sulphate from liquid solutions. Fouling refers to the accumulation of unwanted deposits or impurities on the surfaces of equipment and can lead to reduced process efficiency, increased maintenance and energy consumption, and even equipment damage. When separating Sodium Sulphate from a liquid solution, fouling issues can arise due to various factors, such as scaling1, Impurities2, and chemical reactions3.
Regular cleaning and use of chemicals (scale inhibitors) are common approaches to improve operations, but they often do not yield the desired results. With the KLAREN self-cleaning heat exchanger technology the fouling issues when separating Sodium Sulphate from a liquid solution with evaporators or crystallizers can be mitigated and operation capacity can be kept constant.
Say No to fouling with the KLAREN self-cleaning heat exchanger technology!
1 One of the primary fouling issues in sodium Sulphate separation is the formation of scale. As the solution is concentrated or cooled to crystallize sodium Sulphate, the salt may precipitate and adhere to the surfaces of equipment, such as heat exchangers, pipes, and crystallization vessels.
2 The presence of impurities in the liquid solution can contribute to fouling. These impurities may include other salts, organic compounds, or particulate matter, which can deposit on equipment surfaces during the separation process.
3 Chemical reactions between components in the solution and the equipment surfaces can result in fouling. For example, if the equipment is not made from materials that are resistant to the chemicals in the solution, corrosion and fouling can occur.